In the fulfillment supply chain, you start with efficient order management, utilizing systems to handle and track diverse orders in real-time. Accurate inventory management is essential, using forecasting and tracking systems to meet demand without delays. Warehouse operations require strategic layouts and inventory categorization, guaranteeing quick, safe, and organized processes. Packaging involves selecting proper materials and clear labeling, often automated, to guarantee safe delivery. Shipping and distribution use careful carrier choices and various modes to optimize cost and reach. Finally, last-mile delivery tackles urban congestion and infrastructure challenges, guaranteeing timely delivery. As you explore, deeper insights emerge.
Understanding Order Placement
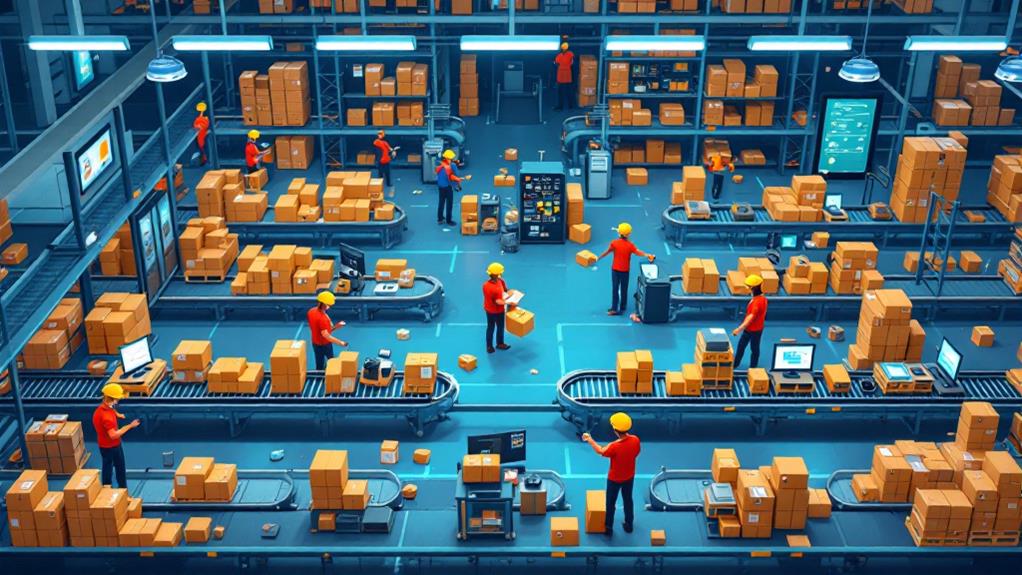
When you grasp the intricacies of order placement, you can greatly enhance the efficiency of your fulfillment supply chain. Understanding this process involves several key components that you need to manage effectively.
First, make sure that your order management system (OMS) is robust and capable of handling a variety of orders, from single-item purchases to bulk shipments. A well-integrated OMS helps streamline communication between sales channels and warehouse operations, reducing errors and delays.
Next, focus on the accuracy of order entry. Mistakes at this stage can lead to major issues down the line, such as incorrect shipments or customer dissatisfaction. Implementing automated systems can minimize human error, while also speeding up the order processing time.
Additionally, consider the importance of real-time tracking. By providing customers with up-to-date information about their orders, you not only enhance their experience but also reduce the burden on customer service teams.
Moreover, establishing clear protocols for order modifications and cancellations can prevent bottlenecks. By setting up a flexible yet structured approach, you can adapt to changes quickly without disrupting the overall flow.
Inventory Management Processes
Effective inventory management processes are essential for guaranteeing a smooth fulfillment supply chain. By keeping a close eye on stock levels, you can avoid both overstocking and stockouts, which can disrupt operations and lead to customer dissatisfaction.
Accurate inventory forecasting is vital; it involves predicting future demand based on historical sales data, seasonal trends, and market analysis. You should implement inventory tracking systems, like barcode scanning or RFID technology, to maintain real-time visibility of your stock.
These systems help you monitor product quantities, locations, and movements within your warehouse, enabling you to make informed decisions. Safety stock, a buffer of extra inventory, is another important consideration, providing a cushion against unexpected demand spikes or supply chain delays.
Cycle counting, a method where you count a small portion of your inventory regularly, guarantees ongoing accuracy without halting operations. This technique helps you identify discrepancies early, reducing errors and enhancing inventory control.
Additionally, you should establish reorder points, specific stock levels that trigger new orders, guaranteeing timely replenishment. By managing these processes effectively, you streamline the supply chain, improve customer satisfaction, and optimize operational efficiency, ultimately contributing to your business's success.
Warehouse Operations Explained
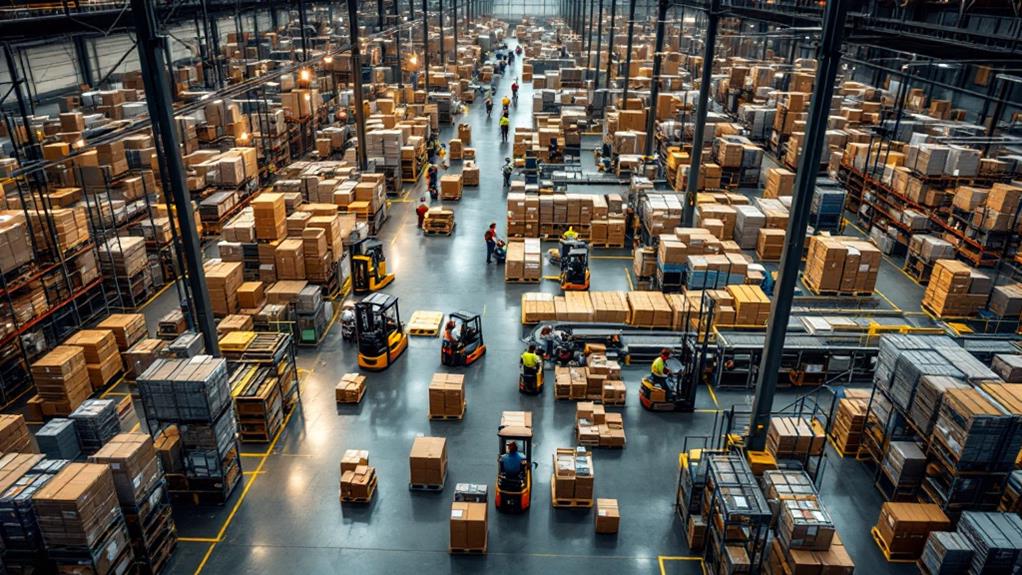
Having a well-organized warehouse is the backbone of a successful fulfillment supply chain. It guarantees efficiency and accuracy in storing and retrieving products. You need to design the warehouse layout strategically, optimizing space and accessibility. Employing a systematic approach, like using vertical storage and narrow aisles, maximizes your storage capacity without sacrificing operational efficiency.
Implementing effective warehouse operations involves several key components. First, inventory tracking systems, such as barcodes or RFID technology, help you maintain real-time visibility of stock levels and locations. This data accuracy prevents stockouts and overstocking, assuring you have the right products available when needed.
Second, categorize your inventory into fast-moving, slow-moving, and seasonal items to enhance picking efficiency. Placing fast-moving items closer to packing stations reduces travel time, speeding up the whole process.
Safety and training are critical. Confirm your team is well-versed in handling equipment, like forklifts and pallet jacks, to prevent accidents. Regular safety audits and staff training sessions contribute to a secure working environment.
Furthermore, maintaining a clean and organized space minimizes errors and boosts productivity. By focusing on these elements, you'll guarantee your warehouse operations run smoothly, supporting the entire supply chain.
Order Processing Workflow
In the domain of fulfillment supply chains, mastering the order processing workflow is vital for customer satisfaction and operational success. This workflow involves several significant steps, each designed to guarantee that orders are accurately received, processed, and prepared for shipment.
First, when an order is placed, it enters your system, triggering an automated response to confirm receipt. This step is essential for keeping customers informed and setting expectations.
Next, inventory allocation takes place where the system checks stock levels to guarantee the ordered items are available. If everything's in stock, the order is queued for picking. This stage involves pulling items from storage locations, which is typically guided by a warehouse management system to optimize efficiency.
In the picking stage, accuracy is paramount. The right items must be selected based on the order details, minimizing the chance for errors. After picking, the items are moved to the packing area, readying them for the next phase.
Key components of the order processing workflow include:
- Order entry and confirmation
- Inventory allocation and verification
- Accurate picking of items
- Efficient movement to packing areas
These steps guarantee a seamless process, minimizing delays and errors, ultimately enhancing the customer experience.
Packaging and Labeling Steps
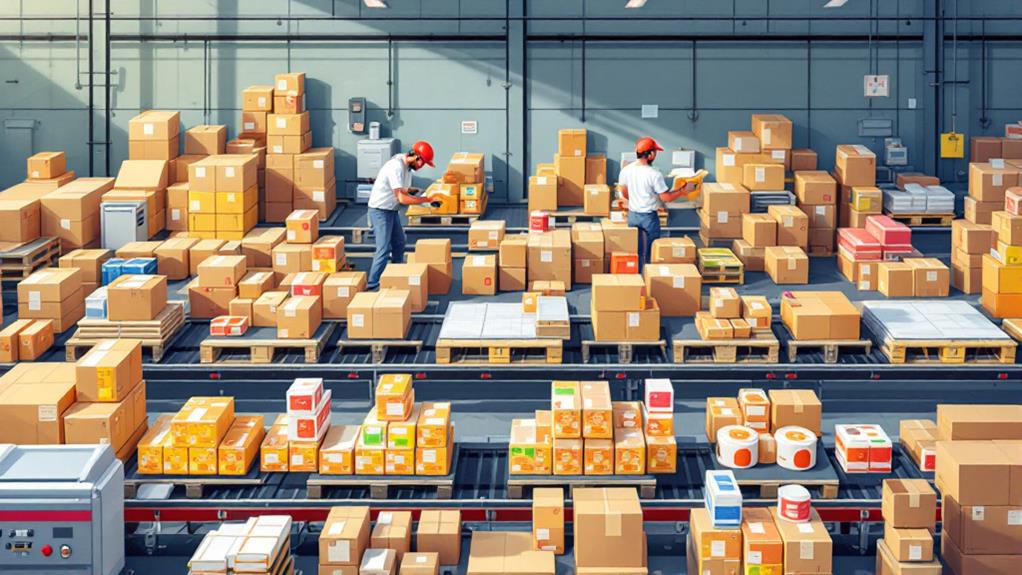
With your items expertly picked and moved to the packing area, it's time to focus on packaging and labeling.
Packaging is vital to protect your products, prevent damage during transit, and guarantee they arrive safely at their destination. Start by selecting the right packaging materials, considering the size, weight, and fragility of each item. Use sturdy boxes, bubble wrap, or foam peanuts to cushion fragile goods. For added security, seal packages with strong packing tape.
Labeling, on the other hand, is significant for accurate delivery. Begin by printing clear shipping labels that include the recipient's address, return address, and a barcode for tracking. Verify labels are legible and securely attached to the package. Double-check each label for accuracy to avoid delivery errors. Incorporate any additional information necessary, such as handling instructions or warning labels, especially for hazardous materials.
Automated systems can streamline these steps, reducing human error and speeding up the process. Consider using software solutions that integrate with your order management system, allowing you to efficiently generate labels and track inventory levels.
Shipping and Distribution Channels
As your packages are prepared and labeled, it's time to focus on the critical next step: selecting the right shipping and distribution channels. Choosing effective channels guarantees your products reach customers efficiently and cost-effectively.
Consider several factors when making this decision, as each can greatly impact your supply chain's performance.
- Carrier Selection: Decide between national carriers like UPS and FedEx, which offer reliability, or regional carriers that might provide cost advantages for local deliveries.
- Shipping Modes: Analyze whether air, sea, or ground transportation fits your needs. Air is fast but costly, sea is economical for large shipments, and ground is versatile for various distances.
- Multi-Channel Distribution: Utilize multiple channels, such as direct-to-consumer and wholesale, to reach different customer segments and maximize market penetration.
- Technology Integration: Implement shipping software to track packages, optimize routes, and streamline operations, guaranteeing real-time updates and improved efficiency.
Understanding these elements helps in crafting a robust shipping strategy, aligning with your business goals and customer expectations.
Last-Mile Delivery Challenges
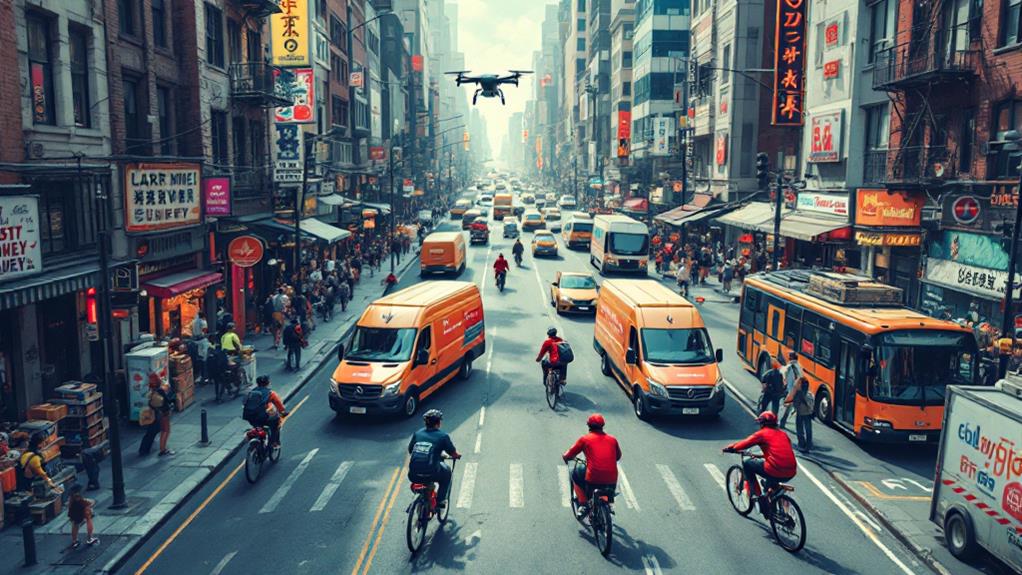
Steering through the intricacies of last-mile delivery poses significant challenges that can impact your overall supply chain efficiency. The last-mile phase, the final step in the delivery process where a package reaches the customer's doorstep, often involves numerous obstacles. Urban congestion can slow delivery times, making timely fulfillment difficult. Maneuvering through traffic-laden streets or narrow lanes in densely populated areas requires strategic planning and can increase operational costs.
Moreover, customer demands for quicker deliveries add pressure. With e-commerce giants setting high standards, consumers now expect same-day or next-day delivery. Balancing these expectations with cost-effective operations is a tricky act.
Another challenge is the unpredictability of delivery locations. You might face difficulties in rural or remote areas where infrastructure is lacking, leading to delays and increased expenses.
Enhancing delivery efficiency requires adopting advanced technologies like route optimization software, which can help reduce delivery times by identifying the most efficient paths. Additionally, employing local delivery hubs or micro-fulfillment centers can bring products closer to customers, reducing transit times.